rms TITANIC,
1911, Cold Starting
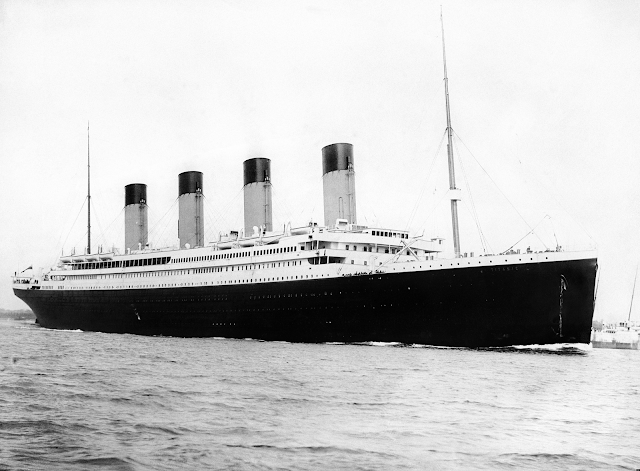
Elevation
of boiler rooms
WHITES STAR
LINE Ltd., Builders: HALAND & WOLFF, Belfast
by Stephen Carey, engineer, editing by Earl of Cruise
by Stephen Carey, engineer, editing by Earl of Cruise
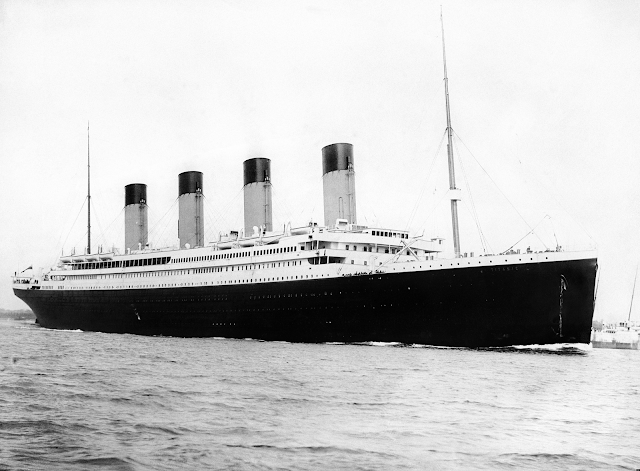
rms TITANIC, 1911 © Stephen Carey
Table
of Contents
1 Overview of machinery spaces
1.1 Boiler rooms
1.2 Coal bunkers
1.1 Boiler rooms
1.2 Coal bunkers
1.3 Propulsion engines
1.4 Electrical power generation
1.4.1 Main generating sets
1.4.2 Emergency generating sets
2 Lighting up the boilers
2.1 Steam line redundancy
3 Starting the generators
3.1 Auxiliary seawater pump and condenser
3.2 Starting an emergency generator
3.3 Starting the main generators
4 Starting main engines
4.1 Main seawater pumps
4.2 Main air pumps (dual system)
4.3 Main Generator exhaust change over
4.4 Main engines
5 The Feedwater and Condensate system
5.1 Surface feed heater
5.2 Contact feed heater
5.3 Boiler Feed Pumps
6 Getting under way
6.1 Low-pressure turbine
1.4 Electrical power generation
1.4.1 Main generating sets
1.4.2 Emergency generating sets
2 Lighting up the boilers
2.1 Steam line redundancy
3 Starting the generators
3.1 Auxiliary seawater pump and condenser
3.2 Starting an emergency generator
3.3 Starting the main generators
4 Starting main engines
4.1 Main seawater pumps
4.2 Main air pumps (dual system)
4.3 Main Generator exhaust change over
4.4 Main engines
5 The Feedwater and Condensate system
5.1 Surface feed heater
5.2 Contact feed heater
5.3 Boiler Feed Pumps
6 Getting under way
6.1 Low-pressure turbine
1.1 Boiler rooms
Titanic
is (or was) a triple screw White Star liner fitted with 5 single-ended and 24
double-ended boilers, operating at 215lb/in2.
These boilers are 5 abreast in 6 boiler rooms, except in No6 Boiler Room
(the foremost one) where the fine lines of the ship only allow 4 abreast.
No1 Boiler Room, forward of the reciprocating engineroom houses the single ended boilers used for hotel services and auxiliary supplies in port. The double-ended boilers are fired for transatlantic passages up to full speed and primarily used for main propulsion.
Stokehold fans provide ventilation for the stokeholds, though for cold starting these cannot be used, as there is insufficient electric supply to run them. The single-ended boilers may be fired on natural draft on cold-start, with the ventilators turned into the wind. If sufficient shore supply is available, a stokehold fan may be able to be started, but it is assumed here that the shore supply only provides lighting and small power. Once under way the vessel operates on induced draft (natural draft) in the same way as a steam locomotive, via large ventilators visible on the upper decks. (See Figure 1)
No1 Boiler Room, forward of the reciprocating engineroom houses the single ended boilers used for hotel services and auxiliary supplies in port. The double-ended boilers are fired for transatlantic passages up to full speed and primarily used for main propulsion.
Stokehold fans provide ventilation for the stokeholds, though for cold starting these cannot be used, as there is insufficient electric supply to run them. The single-ended boilers may be fired on natural draft on cold-start, with the ventilators turned into the wind. If sufficient shore supply is available, a stokehold fan may be able to be started, but it is assumed here that the shore supply only provides lighting and small power. Once under way the vessel operates on induced draft (natural draft) in the same way as a steam locomotive, via large ventilators visible on the upper decks. (See Figure 1)
1.2 Coal bunkers
Coal
bunkers are provided facing the furnaces in each boiler room to enable a ready
supply of coal for the trimmers and firemen to stoke the boilers.
Ash chutes are provided to discharge ash from the furnace bottoms overboard at regular intervals to keep the stokehold clear of ash whilst at sea. In port ash hoists are used to dispose of the ash to shore facilities.
The main steam pipes run the length of the boiler rooms into the reciprocating engineroom for distribution to the engines and auxiliaries.
Ash chutes are provided to discharge ash from the furnace bottoms overboard at regular intervals to keep the stokehold clear of ash whilst at sea. In port ash hoists are used to dispose of the ash to shore facilities.
The main steam pipes run the length of the boiler rooms into the reciprocating engineroom for distribution to the engines and auxiliaries.
1.3 Propulsion engines
There
are two triple-expansion reciprocating engines situated in the reciprocating
engineroom, aft of Boiler Room No1.
Steam from the main steam piping is admitted to the reciprocating engines
which, whilst manoeuvring in port, exhaust direct to the vacuum main
condenser. Once Full Away on Passage,
large changeover valves redirect the exhaust steam from the reciprocating
engines into the low-pressure turbine situated in the turbine engineroom aft of
the main engineroom, separated by a watertight bulkhead.
Exhaust steam from the turbine is directed to the vacuum condensers where it is condensed into water (termed condensate) and pumped back into the boilers – see later. (See Figure 6)
Exhaust steam from the turbine is directed to the vacuum condensers where it is condensed into water (termed condensate) and pumped back into the boilers – see later. (See Figure 6)
1.4 Electrical power generation
1.4.1 Main generating sets
The
vessel is fitted with 4 400kW main generators driven by steam reciprocating
prime movers. Reduced steam at a
pressure of 185lb/in2 (12.75 bar) is fed to the engines and exhaust steam is
directed - in port or at start up - to the auxiliary condenser. At sea the generator exhaust steam is
directed to the surface feed heater to extract the remaining energy from the
exhaust steam and deliver it to the feed heating system. This configuration gives a total installed
power of 1.6MW dc, with three sets covering the full steaming load and one in
stand-by. (See Figure
3)
1.4.2 Emergency generating sets
These are
termed Emergency/Auxiliary Generating Sets but as they are steam driven, are
not able to be cold-started without a steam supply. There are two of these sets, situated above
the waterline on a flat within the engine casing on the Shelter or D Deck, each
of 30kWdc output power. To give a certain
amount of redundancy, they are fed by separate steam pipes from three of the
boiler rooms (see Figure
1).
With the ship on shore power we will be using these two machines to start up the ship’s lighting systems in order to disconnect the shore power as soon as possible.
This start-up routine assumes the emergency sets as the quickest method of getting off shore power and on to ship’s power, but it could be that the engineers would cut out this stage and just start the main generating sets, though the time taken would probably be a lot longer.
With the ship on shore power we will be using these two machines to start up the ship’s lighting systems in order to disconnect the shore power as soon as possible.
This start-up routine assumes the emergency sets as the quickest method of getting off shore power and on to ship’s power, but it could be that the engineers would cut out this stage and just start the main generating sets, though the time taken would probably be a lot longer.
2 Lighting up the boilers
With the
lights on shore power so we don’t have to use torches, the firemen are set to
work in the required boiler rooms to lay fires in sufficient boilers to provide
enough steam for the generators. Once
lit, the boiler draft is adjusted by dampers using natural (induced) draft and
the fires start to heat the water in the fire-tube boilers. Water-tube boilers are much more efficient
and faster starting than fire-tube, but hadn’t been invented at this time. It would take around 7 – 12 hours to warm
through and start to raise sufficient steam.
Raising steam too quickly in a cold boiler can lead to thermal stress
which is not good for the boiler longevity and could even cause cracking and
rupture, especially on riveted boilers.
At the same time, the number of boilers required for sailing are also laid and lit.
The emergency generators are available for starting with a steam pressure of 185lb/in2.
After some hours raising steam we have around 190lb/in2 in the first boilers to be lit. Most probably boiler rooms 6 and 5 would come on line first as they are the furthest forward, No 6 being open to the main steam lines for warming through, No 5 open to the emergency generator independent line (see Figure 1). Steam is raised on these boilers with the main stop valves open such that the whole system is taken up to pressure, with all the main steam line drain valves open one to two turns right back to the engineroom bulkhead stops. This same principle applies to steam systems today. Further boiler stop valves are cracked open once up to pressure.
Note:
At the same time, the number of boilers required for sailing are also laid and lit.
The emergency generators are available for starting with a steam pressure of 185lb/in2.
After some hours raising steam we have around 190lb/in2 in the first boilers to be lit. Most probably boiler rooms 6 and 5 would come on line first as they are the furthest forward, No 6 being open to the main steam lines for warming through, No 5 open to the emergency generator independent line (see Figure 1). Steam is raised on these boilers with the main stop valves open such that the whole system is taken up to pressure, with all the main steam line drain valves open one to two turns right back to the engineroom bulkhead stops. This same principle applies to steam systems today. Further boiler stop valves are cracked open once up to pressure.
Note:
Whilst the single ended boilers in Boiler
room No1 were normally used in port, at the time of the sinking these boilers
were apparently not lit, so must have been shut down on sailing from the last
port (Queenstown).
2.1 Steam line redundancy
For
redundancy in main steam lines (Figure
1) -
The main generators, refrigeration machinery and auxiliary pumps (termed “the auxiliaries”) were fed from a steam main connected to -
· Starboard outer pair of boilers in Boiler Room 4
The main generators, refrigeration machinery and auxiliary pumps (termed “the auxiliaries”) were fed from a steam main connected to -
· Starboard outer pair of boilers in Boiler Room 4
· Port outer pair of boilers in Boiler Room 2
· All five single-ended boilers in Boiler Room 1
The main generators were fed exclusively from a steam main connected to -
· Port outer pair of boilers in Boiler Room 2
· All five single-ended boilers in Boiler Room 1 (the line used for electrical power in port)
The emergency generators were connected to -
· All five boilers in Boiler Room 5
· All five boilers in Boiler Room 3
· All five boilers in Boiler Room 2
· An auxiliary line from the main steam lines feeding the reciprocating engines in the engineroom
· All five single-ended boilers in Boiler Room 1
The main generators were fed exclusively from a steam main connected to -
· Port outer pair of boilers in Boiler Room 2
· All five single-ended boilers in Boiler Room 1 (the line used for electrical power in port)
The emergency generators were connected to -
· All five boilers in Boiler Room 5
· All five boilers in Boiler Room 3
· All five boilers in Boiler Room 2
· An auxiliary line from the main steam lines feeding the reciprocating engines in the engineroom
The emergency
engines were run regularly to keep the steam lines warmed through in case of
emergency.
Note on the sinking:
As the vessel started to plunge by the
head, to conserve steam and keep the lights on as long as possible, the main
generators would have been fed from the furthest aft steam line, that from
Boiler Room 2 above. As Boiler Room 5
fires were drawn, the steam from the boilers would start to decay, and the
isolation from them to the main steam lines and the line to the emergency
generators would have been shut off.
As each boiler room flooded and was shut down, the lines from each boiler would be isolated. The steam reserve in boiler rooms 3 and 2 (Boiler Room 1 was apparently not fired at the time according to the enquiry) would have supplied both the main and emergency generators, and as the latter had a smaller steam consumption it is likely that the main generators would have been shut down and the auxiliaries used to conserve what steam was left in the boiler drums.
Boiler Room 2 was the furthest aft and would have been supplying steam until the end, the auxiliary seawater pump and air pump fed from the port outer pair of boilers, and the emergency generators from all five boilers, though more probably the remaining three in order to separate the auxiliary pumps from the emergency generators.
For an illustration of the steam lines, on the
next page is the general layout, Copyright Sam Halpern from the Titanic site -
www.titanicology.com where
a fuller description of the steam system may be found.As each boiler room flooded and was shut down, the lines from each boiler would be isolated. The steam reserve in boiler rooms 3 and 2 (Boiler Room 1 was apparently not fired at the time according to the enquiry) would have supplied both the main and emergency generators, and as the latter had a smaller steam consumption it is likely that the main generators would have been shut down and the auxiliaries used to conserve what steam was left in the boiler drums.
Boiler Room 2 was the furthest aft and would have been supplying steam until the end, the auxiliary seawater pump and air pump fed from the port outer pair of boilers, and the emergency generators from all five boilers, though more probably the remaining three in order to separate the auxiliary pumps from the emergency generators.
Figure 1 rms TITANIC Steam line redundancy © Sam Halpern
3 Starting
the generators
3.1 Auxiliary seawater pump and condenser
In
order to start an emergency generator, the exhaust steam from the engines is
directed to the auxiliary condenser. The
seawater passing through this condenser condenses the exhaust steam into water
(termed “well condensate”), thereby drawing a vacuum. Without this the engine would trip on high
exhaust backpressure, as the exhaust steam otherwise has nowhere to go. In addition the condenser is fitted with an
auxiliary air pump (or vacuum pump) to increase the vacuum by removing
non-condensables such as air, in order to drop the exhaust steam pressure
further.
The auxiliary seawater pump is steam driven and situated under the auxiliary condenser on the starboard side of the main engineroom. (See Figure 6)
With the drains open, steam is admitted to the pump, which circulates seawater through the auxiliary condenser to overboard. In the same way the auxiliary air pump is started in order to draw a vacuum. We are now ready to start an emergency generator
The auxiliary seawater pump is steam driven and situated under the auxiliary condenser on the starboard side of the main engineroom. (See Figure 6)
With the drains open, steam is admitted to the pump, which circulates seawater through the auxiliary condenser to overboard. In the same way the auxiliary air pump is started in order to draw a vacuum. We are now ready to start an emergency generator
3.2 Starting an emergency generator
With
all the drains open, steam is admitted to the reciprocating engine, with the
exhaust going to the auxiliary condenser.
Once the engine has warmed through and is running at the rated speed of
380rev/min, we go to the main switchboard where the main breaker for the emergency
generator is situated. As the vessel is on
shore power, the breaker is closed onto the emergency board. Even if other generators are on the board,
with Direct Current no synchronisation is required, hence generators can be
added to the main switchboard at any given time. On closing the breaker, the voltmeter lamps
will light dimly and show a small voltage.
Using the shunt field regulator (also called the exciter), we turn up
the voltage until it shows full mains voltage of 100V.
We now have 30kW of power available – 60kW if we start both generators - and can start to get main power on. The shore power can be disconnected.
A note on the sinking here – the lights would have stayed on providing an emergency generator was running, which is likely to have been the case as there were no batteries fitted for emergency lighting on Titanic, though Olympic may have been retrofitted after the accident. Looking at the angle of the waterline at the point where the lights went out – just prior to breaking in two – it is very close to the suction for the auxiliary condenser seawater pump above. With an emergency generator and the seawater and air pumps running on the volume of steam left in the boilers that remained un-flooded, there would have been little or no reason for any of the engineering staff to remain below, apart from perhaps the Chief Engineer and a couple of volunteers to swing isolation valves, reset breakers etc. None of the boilers would have been stoked at this point, as the fires would have been drawn and the stokers sent up on deck, and indeed many of the stokers survived the sinking. One or more of the witnesses stated that most of the engineers – including the Second, Farquharson - were seen on deck prior to the sinking, though none survived. Once the seawater induction for the auxiliary seawater pump came out of the water, the generator would have immediately stopped on high back-pressure, and the lights would have gone out.
We now have 30kW of power available – 60kW if we start both generators - and can start to get main power on. The shore power can be disconnected.
A note on the sinking here – the lights would have stayed on providing an emergency generator was running, which is likely to have been the case as there were no batteries fitted for emergency lighting on Titanic, though Olympic may have been retrofitted after the accident. Looking at the angle of the waterline at the point where the lights went out – just prior to breaking in two – it is very close to the suction for the auxiliary condenser seawater pump above. With an emergency generator and the seawater and air pumps running on the volume of steam left in the boilers that remained un-flooded, there would have been little or no reason for any of the engineering staff to remain below, apart from perhaps the Chief Engineer and a couple of volunteers to swing isolation valves, reset breakers etc. None of the boilers would have been stoked at this point, as the fires would have been drawn and the stokers sent up on deck, and indeed many of the stokers survived the sinking. One or more of the witnesses stated that most of the engineers – including the Second, Farquharson - were seen on deck prior to the sinking, though none survived. Once the seawater induction for the auxiliary seawater pump came out of the water, the generator would have immediately stopped on high back-pressure, and the lights would have gone out.
3.3 Starting the main generators
Using
the power available from the emergency generator(s) we can now start the
stokehold fan for the stokeholds where fires are lit, which will make it easier
to get the boilers up to pressure and make it more bearable for the stokers. As we are consuming steam, we will also be
able to start a main feed pump to supply the boilers with feed water as
required, described later under the feed system.
The generators are forced lube type, so first we start a LO pump (again steam driven, as are all the engineroom auxiliaries) in the usual way. Presumably all the exhausts, from any auxiliary pumps that are started prior to getting the main condensers on line, are sent to the auxiliary condenser.
After warming through the steam lines and opening the engine exhaust to the auxiliary condenser, the first and subsequent generators are warmed through and run up to a speed of 325rev/min. It is not known how many generators would run on the auxiliary condenser, but as the reference work states this was the condition in port, it was likely to be able to run at least two. Without an electrical single line diagram or load estimate, we have to rely on conjecture.
On the main generator control panel, the breaker is closed for the generator in question and the shunt field regulator adjusted to give mains voltage. The breaker(s) for the emergency generator(s) may be opened at this stage and the emergency set(s) shut down, though kept warmed through for immediate start on failure of the main sets. (See Figure 5)
We can now put the other generator(s) on the board as required. We are up and running and can connect other feeders via the main switchboard distribution (see Figure 4).
As you can see, this is quite a long job compared to a modern diesel powered ship (though steamships still take some time). A blackout on a modern motorship can be restored within a few minutes, though cold-starting takes longer depending on generator warming through requirements.
The generators are forced lube type, so first we start a LO pump (again steam driven, as are all the engineroom auxiliaries) in the usual way. Presumably all the exhausts, from any auxiliary pumps that are started prior to getting the main condensers on line, are sent to the auxiliary condenser.
After warming through the steam lines and opening the engine exhaust to the auxiliary condenser, the first and subsequent generators are warmed through and run up to a speed of 325rev/min. It is not known how many generators would run on the auxiliary condenser, but as the reference work states this was the condition in port, it was likely to be able to run at least two. Without an electrical single line diagram or load estimate, we have to rely on conjecture.
On the main generator control panel, the breaker is closed for the generator in question and the shunt field regulator adjusted to give mains voltage. The breaker(s) for the emergency generator(s) may be opened at this stage and the emergency set(s) shut down, though kept warmed through for immediate start on failure of the main sets. (See Figure 5)
We can now put the other generator(s) on the board as required. We are up and running and can connect other feeders via the main switchboard distribution (see Figure 4).
As you can see, this is quite a long job compared to a modern diesel powered ship (though steamships still take some time). A blackout on a modern motorship can be restored within a few minutes, though cold-starting takes longer depending on generator warming through requirements.
4 Starting main engines
We
now have power for firing all the boilers necessary for starting the main
engines and getting the engineroom ready for sea.
First we have to get the exhaust steam system arranged in a similar way to that of the generators, but in the case of the main engines, the auxiliary condenser is nowhere near big enough to handle the exhaust from a main engine.
For this we need to start to draw a vacuum on the main condensers of which there are two, one either side of the low-pressure turbine in the turbine room.
First we have to get the exhaust steam system arranged in a similar way to that of the generators, but in the case of the main engines, the auxiliary condenser is nowhere near big enough to handle the exhaust from a main engine.
For this we need to start to draw a vacuum on the main condensers of which there are two, one either side of the low-pressure turbine in the turbine room.
4.1 Main seawater pumps
As
with the auxiliary condenser, we need seawater to condense the steam in order
to create a vacuum and drop its pressure to avoid exhaust backpressure on the
engines. These pumps are pretty huge and
are driven by compound steam engines.
There are two pumps per condenser (total of four) arranged adjacent to
the condensers in the turbine engineroom.
(See Figure
6)
As with all steam engines, these are first warmed through with the drains open, then slowly started up until they are at full revs. Once the pumps are started, seawater passes through the condensers and discharges overboard – that’s the large discharge that can be seen on any steamship up to the present day. As a guide, the amount of seawater required to condense the steam is 50 to 80 times the steam flow. With the reciprocating engines running at 75 revolutions per minute and 24 double-ended boilers on line, a supply rate of just over 260lbs of steam per minute per boiler would be produced, or 260x24x60=374400lbs/hr. The amount of seawater would therefore be 50 to 80 times this amount, 8,300 to 13,300t/hr – very large pumps.
As with all steam engines, these are first warmed through with the drains open, then slowly started up until they are at full revs. Once the pumps are started, seawater passes through the condensers and discharges overboard – that’s the large discharge that can be seen on any steamship up to the present day. As a guide, the amount of seawater required to condense the steam is 50 to 80 times the steam flow. With the reciprocating engines running at 75 revolutions per minute and 24 double-ended boilers on line, a supply rate of just over 260lbs of steam per minute per boiler would be produced, or 260x24x60=374400lbs/hr. The amount of seawater would therefore be 50 to 80 times this amount, 8,300 to 13,300t/hr – very large pumps.
4.2 Main air pumps (dual system)
The
air pumps (called vacuum pumps these days) evacuate air and water from the
condensers, with the air pumps extracting non-condensables and helping the
vacuum in so doing. This improves the
exhaust flow through the engines and also extracts the maximum energy from the
steam. They are situated in the turbine room by the condensers and are of
course steam driven. They are started in
the usual way, and left to draw a vacuum on the condensers, usually around
28.5in with an atmospheric pressure of 30in. In modern day parlance these dual air-water
pumps would be termed vacuum pumps and condensate pumps respectively.
In Figure 6 they can be seen inboard of the two condensers in the turbine room. Condensate from the water side of the pumps is returned to the condenser or to the feed tank against the forward bulkhead in order to maintain the condenser level, with air being ejected to atmosphere. From these tanks the water runs to the hotwell tanks under the hotwell pumps either side in the main engineroom, of which more later.
In Figure 6 they can be seen inboard of the two condensers in the turbine room. Condensate from the water side of the pumps is returned to the condenser or to the feed tank against the forward bulkhead in order to maintain the condenser level, with air being ejected to atmosphere. From these tanks the water runs to the hotwell tanks under the hotwell pumps either side in the main engineroom, of which more later.
4.3 Main Generator exhaust change over
Now
that the steam and feed system is up and running, we can extract the energy
from the main generator engine exhaust by
redirecting the steam to the surface shell and tube feed water heater
shell, through the tubes of which the feedwater from the hotwell tank passes
via the hotwell pumps on its way to the main feed pumps. This imparts heat to
the feed water to avoid wasting the energy from the generator exhaust.
4.4 Main engines
By
this time the engineers (we assume we are not doing this on our own) will have
engaged the steam turning gear on both engines, and are oiling round the main,
connecting and crosshead bearings, as well as starting the forced lube oil
pumps. Titanic’s engines are open
crankcase, so oil is directed to oil pots when the engine is running by skilled
oilers. The cylinder oilers are also
filled and set up to admit cylinder oil in a controlled amount. After turning the engine, the turning gear is
taken out to avoid damage when the engine starts.
Steam is admitted to the engines with the drains full open and the exhausts open via the changeover valves direct to the condensers. At first the main steam bulkhead stop valves are cracked open until everything is warmed through, whence they can be fully opened.
Once the cylinder drains are emitting steam, we can call the bridge and ask if the propellers are clear for a slow turn ahead and astern. Once this is given, the reversing gear is set to full ahead and the main steam valve control valve cracked open. The engine will start to turn ahead at low revs. After a few turns ahead the control valve is closed and the reversing gear set to astern position. Again the control valve is cracked open and the engine turned astern for a few revs at low speed.
We are about ready to go, and test the communications between the engineroom, boiler rooms and bridge that we are ready for sea service. Around the same time an engineer is dispatched to the steering engine room to warm through the steam steering engines and test the rudder from midships to 30 degrees port, back to 30 degrees starboard then returning to midships.
Steam is admitted to the engines with the drains full open and the exhausts open via the changeover valves direct to the condensers. At first the main steam bulkhead stop valves are cracked open until everything is warmed through, whence they can be fully opened.
Once the cylinder drains are emitting steam, we can call the bridge and ask if the propellers are clear for a slow turn ahead and astern. Once this is given, the reversing gear is set to full ahead and the main steam valve control valve cracked open. The engine will start to turn ahead at low revs. After a few turns ahead the control valve is closed and the reversing gear set to astern position. Again the control valve is cracked open and the engine turned astern for a few revs at low speed.
We are about ready to go, and test the communications between the engineroom, boiler rooms and bridge that we are ready for sea service. Around the same time an engineer is dispatched to the steering engine room to warm through the steam steering engines and test the rudder from midships to 30 degrees port, back to 30 degrees starboard then returning to midships.
5 The Feedwater and Condensate system
Condensate
from the bottom well of the condensers is pumped via the water-side of the dual
pumps into the feed tanks on the forward bulkhead of the condenser room. From there it drains to the hotwell tanks either
side in the forward engine room.
The hotwell pumps draw from this tank and pump the feedwater through two feed heaters, after first sending it through filters to remove oil, grease and other impurities.
The hotwell pumps draw from this tank and pump the feedwater through two feed heaters, after first sending it through filters to remove oil, grease and other impurities.
5.1 Surface feed heater
The
first is a shell and tube surface feed heater, where the feedwater passes
through the tubes. As mentioned above,
the exhaust steam from the main generators at about 5psia passes through the
shell of this heater, and imparts its energy to the feedwater, raising it from
around 70°F to 140°F, the exhaust condensate from the shell is pumped into the
feed downstream of the heater by a mono air pump.
5.2 Contact feed heater
The
2nd of the two feed heaters is a contact heater where the feedwater
comes in contact with exhaust steam from the many engineroom auxiliary pumps and
refrigeration units. It is situated high
in the engineroom on D Deck and acts as a deaerator once the air vent at the
top of the heater is opened up to the main condenser to extract non-condensable
gases (CO2 and O2), which can cause corrosion problems in the boilers. This exhaust steam input condenses in the
feedwater stream – thereby adding it directly into the feedwater - and raises
the temperature of the feed water from 140°F to 230°F. At low load it may
be necessary to use live steam into the heater, depending on the energy
available from the auxiliaries.
5.3 Boiler Feed Pumps
From
the contact heater the feed water is then extracted under gravity by the main
feed pumps and sent to the boilers as required.
Titanic did not have automatically operating feed control valves, so
this was a manual operation. The height of the contact heater ensures that
there is sufficient positive suction head for the main feed pumps that feed the
boilers. In Figure
2 is a schematic of the propulsion steam, feed and
condensate system described above, © Sam Halpern.
All is now ready to go, with the stokers bending their backs to raise steam on all the boilers required for leaving port.
All is now ready to go, with the stokers bending their backs to raise steam on all the boilers required for leaving port.
Figure 2 rms TITANIC Propulsion steam, feed and
condensate system, © Sam Halpern
6 Getting under way
In
response to the bridge signals on the engineroom telegraphs, the main engines
are manoeuvred accordingly and the ship departs her berth and heads for the
open sea.
6.1 Low-pressure turbine
Once
the ship is up to 50% power or more ahead, and prior to full away, the
low-pressure turbine is warmed through, with its exhaust directed to the two
condensers. At the moment the main
engines are exhausting direct to the condenser, so we operate the huge
changeover valves (themselves steam engine driven as they are so big – see Figure 6) - to direct the exhaust steam from the engines to
the low-pressure turbine, on the shaft of which is the centre propeller. The turbine will work up to speed, governed by
the exhaust steam pressure.
The main engine exhausts are now driving the low-pressure turbine and full power can be worked up once full away is rung on the telegraphs. This novel method of propulsion is quadruple expansion, with triple expansion through the reciprocating engines, and the final 4th expansion through the turbine. It was considered to be an economical method in such a big ship and indeed by the end of her life, the Olympic was performing better than she had when new, with a much lower fuel consumption than the Mauretania (turbine driven) which was a much smaller ship, and only 2knots faster than Olympic; quite a price to pay for an extra 48 miles per day.
We’re done, we’ve been down below on a coal-burner for over 12 hours, and it’s time to go to bed before having to get up again and lose our lives as the ship goes down.
The main engine exhausts are now driving the low-pressure turbine and full power can be worked up once full away is rung on the telegraphs. This novel method of propulsion is quadruple expansion, with triple expansion through the reciprocating engines, and the final 4th expansion through the turbine. It was considered to be an economical method in such a big ship and indeed by the end of her life, the Olympic was performing better than she had when new, with a much lower fuel consumption than the Mauretania (turbine driven) which was a much smaller ship, and only 2knots faster than Olympic; quite a price to pay for an extra 48 miles per day.
We’re done, we’ve been down below on a coal-burner for over 12 hours, and it’s time to go to bed before having to get up again and lose our lives as the ship goes down.
RIP
Titanic.
Plates from the publication “Ocean Liners of the Past,
Olympic & titanic (1911)
(With notes to explain the various items of equipment fitted)
(With notes to explain the various items of equipment fitted)
Figure 3 rms TITANIC Boiler Rooms 1
& 2
Here
you can see the No 1 Boiler Room single-ended boilers with the coal bunker
forward, opposite the furnaces.
Also shown is the main steam pipe that is routed throughout the ship from No6 Boiler Room (foremost) to the engineroom.
On the deck above can be seen the Sirocco fans that are used for ventilation of the stokeholds. The boilers themselves are fired on “Natural Draft”, with the stokehold pressurised by the fans. Where the combustion air is ducted via trunking into the boiler furnace, this is termed “Forced Draft”, as employed on Cunard vessels of the era.
Also shown is the main steam pipe that is routed throughout the ship from No6 Boiler Room (foremost) to the engineroom.
On the deck above can be seen the Sirocco fans that are used for ventilation of the stokeholds. The boilers themselves are fired on “Natural Draft”, with the stokehold pressurised by the fans. Where the combustion air is ducted via trunking into the boiler furnace, this is termed “Forced Draft”, as employed on Cunard vessels of the era.
Electrical
Generating Room
Figure 4 rms TITANIC Electrical Generating Room
This
view shows the main generator room with the 4 x 400kW generator sets. You can see the three propeller shafts
passing through this room in the views.
In the profile view you can see the main switchboard gallery above the sets. Engineers on watch can see from there down to the generators.
In the profile view you can see the main switchboard gallery above the sets. Engineers on watch can see from there down to the generators.
Figure 5 rms TITANIC Sectional View of Main Generator Set
This
is a compound reciprocating crosshead type engine driven DC generator of 400kW. The emergency sets are similar though
smaller.
Main
switchboard in the electrical shop
Figure 6 rms TITANIC Main
Distribution Switchboard
This
view of the main switchboard in the assembly shop shows the extent of the
electrical distribution around the ship.
At the top are the breakers, under them the voltmeters and ammeters, and below them the large porcelain fuses.
At the top are the breakers, under them the voltmeters and ammeters, and below them the large porcelain fuses.
Main
Generator Control Panel and Breakers
Figure 7 rms TITANIC Main Generator
Breaker Control Panel
Unlike
more modern ac and dc switchboards which have the generator breakers integrated
with the switchboard, Titanic’s generators had their on control panel and
breaker switches. The shunt field
regulators for increasing and decreasing the voltage are on this panel, which
is for two of the main generator sets.
Plan of Engine Rooms
Figure 8 rms TITANIC Main and
Turbine Engine Rooms
Zoom
in to see this picture more clearly.
In the main engineroom can be seen:
1. The two reciprocating main engines arranged
port and starboard, with the steam lines coming through the watertight bulkhead
aft of No1 Boiler Room
2. The auxiliary condenser with the auxiliary
seawater circulating pump situated below it
3. The hotwells and hotwell pumps that
transfer the feed water to the feed heaters via the filters, seen against the
forward bulkhead port and starboard
4.
The auxiliary air pump that creates a
vacuum on the auxiliary condenser
5. The main feed pumps that draw from the
contact feed heater above the engineroom and discharge to the boiler feed lines
and thence to the boilers
6.
Auxiliary pumps such as forced lube oil,
bilge, ballast, fire and general service
7.
Refrigeration machinery on the port side
outboard
In the turbine room can be seen:
1. The low pressure turbine driving the centre
propulsion shaft and propeller
2. The huge changeover valves to divert
exhaust steam from the main engines to either the condensers direct, or via the
low-pressure turbine. The arms shown on
top of the valves are part of the steam driven machinery that operates them as
they cannot be shifted manually
3. The main condensers either side of the
turbine
4. The main seawater circulating pumps
outboard on both sides
5. Condenser feedwater tanks
6.
Dual water-air pumps (condensate and vacuum
pumps)
Written by Stephen Carey
This Starting from cold series are awesome. I would like to see some other all-timers like the Queen Mary, the QE2 or even the QM2 (and of different workings) in the series and then all of that turned into a book. It would be a piece for collection !
ReplyDelete